Wet Milling vs Dry Milling: The Differences, …
See more on hockmeyer
Explore further
The Differences between Dry Milling and Wet MillingWEBThis study investigates the effect of using ethanol as the process control agent during the wet ball milling of niobium (Nb).
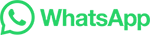