Modelling the Specific Grinding Energy and Ball-Mill …
Abstract. We propose a new model for the prediction of the specific grinding energy, which proved to approach very well the values calculated with the help of the …
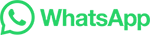
Abstract. We propose a new model for the prediction of the specific grinding energy, which proved to approach very well the values calculated with the help of the …
However, this still has to be transferred to the breakage environment within the comminution device. An approach is proposed in Section 7.1 with the mechanistic ball mill model. 6. Application to specific comminution devices. The process of comminution requires staged size reduction, with a series of devices each targeting a range of size ...
Volume-specific mill power and energy form the basis of the model. ... The energy efficiency of ball milling in comminution. Int. J. Miner. Process. (2002) D. Tromans ... Powder Technology, Volume 286, 2015, pp. 610-615. Okay Altun, …, Udo Enderle. Energy absorption in particle breakage under impact load.
The net specific energy of the Bond ball mill is then calculated from the ratio of the net energy to the circuit new feed rate, taking account of the 250% circulating load. ... Napier-Munn, T.J., Morrell, S., Morrison, R.D., Kojovic, T., 1996. Mineral comminution circuits: their operation and optimisation. ISBN 0 646 28861 x. Julius ...
The characteristic particle size D 80 gradually decreased and the reduction ratio gradually increased with the increase in specific energy consumption. The specific energy consumption of high voltage pulse discharge breakage was described by the Walker theory (E = 215.13 × (1 x 0.33-1 12 0.33)). Besides, the high voltage pulse …
An Energy-T_75 Size Reduction Model for Ball Mills. Jiaqi Tong Caibin Wu Ningning Liao Chengfang Yuan Zhilong Cheng Chong Zeng. Materials Science, Engineering. Mining, Metallurgy & Exploration. 2022. In a series of Julius Kruttschnitt size-dependent breakage models, the cumulative percentage passing 1/10 of the initial size is used as a ...
Specific grinding energy w from Denver slide rule (kwh/s.t.) 13 POWER DRAW P OF DENVER BALL- MILLS z With application of linear least squares regression to 45 pairs (P, D2.5×L) obtained from Denver slide rule, the linear equation, without the constant term (y=bx), is: P = 12.767 D L (hp) or 2.5 P = 9.524 D L (kw) 2.5 But since P = kρf (1 − ...
providing operating data for 3 semi -autogenous grinding (SAG) mills and 4 ball mills. Results show on. average that 7 9% of the supplied electrical energy converts to heat absorbed by the slurry ...
Abstract. Comminution, particularly milling, is on average the largest consumer of energy in mining. Actual comminution circuits consist in most of the cases …
The size-energy relationships in comminution are useful models that relate the energy requirements of a process to the changes in size of the particles. In the generalized theory, the energy is a function of powers of the initial and of the final size. Because of the form of the generalized size-energy relationship, it is possible to relate it …
A comminution circuit of three-stage crushing and one-stage milling was adopted by configuring the tower mill after HPGR. As shown in Fig. 1, the primary crushing involves a C80 Jaw crusher comminuting the ROM ores from − 350 to − 70 mm for feeding the secondary crushing.In secondary crushing, a GP100M cone crusher is closed with a …
An approach has been formulated in which the specific energy requirements of comminution circuits containing conventional crushers, HPGRs and tumbling mills can be predicted. ... 2011) and hence need less ball mill power. Based on data from Koski et al. (2011) and Kock et al. (2015) a ball mill in a HPGR-Ball mill circuit will need about 20% ...
The Coalition for Energy Efficient Comminution ... A new general formula to predict the specific energy of grinding in ball mills and vertimills. Pechea. Published in Proceedings of the IMPC2020 Congress, SAIMM ... involving ball mills and vertimills in different configurations over a wide range of feed and product sizes, work indices and mill ...
The ball milling requirements of HPGR and standard crusher products are measured.. Methods for assessing the energy consumption of the Bond Ball Mill are discussed. • The average reduction in Work Index of HPGR products was 1.9 kWh/t.. A similar magnitude of reduction was observed in the Size Specific Energy.. Ball milling …
This paper proposes the use of the energy required to produce new − 75 μm material (hereafter referred to as size specific energy or SSE after (Powell et al., 2003–2010)) as a simplified measure across a broader range of particle sizes. Hukki (1979) first introduced this method to characterise the efficiency of closed grinding circuits. …
Different possibilities to define energy efficiency: 1. Specific energy of mill compared to new created surface energy → not meaningful, efficiency much smaller that 1% 2. …
A method for predicting the specific energy requirement of comminution circuits and assessing their energy utilisation efficiency. Miner. Eng. ... ball mills (Silva and Casali, 2015). Another argument for the usage of beater mills over ball mills is the low number of collisions with sufficient energy to cause breakage that occurs in the later ...
Since the grinding specific energy is a function of feed rate and related ... Hall, R.: Analyses of the Total Required Energy for Comminution of Hard Ores in Sag Mill and Hpgr Circuits, pp. 129–138 (2008) ... Cervellin, A., Burns, F., Musa, F.: Comparison of energy efficiency between ball mills and stirred mills in coarse grinding. Miner. Eng ...
A specific energy-based size reduction model for batch grinding ball mills was reported in a previous paper (Shi and Xie, 2015). A discharge function modified from the Whiten …
The energy to do so is also one of the largest costs of any industrial plant, and so comminution tests were established to predict those energy requirements and associated costs to power the crushers and mills. ...
In his approach the total specific energy of the entire AG/SAG circuit is firstly predicted using the SAG mill feed F80 and the ball mill cyclone overflow P80. Morrell's model (Morrell, 2011) relates the feed, mill geometry and operating conditions to the specific energy of the circuit. However, the F80 is not enough to represent properly ...
A new general formula to predict the specific energy of grinding in ball mills and vertimills - CEEC (Coalition for Eco Efficient Comminution) Pechea. Published in Proceedings of …
The total circuit specific energy is calculated using an approach that was also standardised by the GMG (2016). However, the SAG mill specific energy is calculated using …
A method for predicting the specific energy requirement of comminution circuits and assessing their energy utilisation ... the final product P80 normally reached by conventional ball mills (fine ...
A particle size reduction model has been developed as the first component of an upgraded ball mill model. The model is based on a specific energy-size reduction function, which calculates the particle breakage index, t 10, according to the size-specific energy, and then calculates the full product size distribution using the t 10-t n relationships and the mass …
The grinding action (attrition), vertical arrangement, and finer media size distribution means that Vertimills offer an average energy saving of 30-50% compared with ball mills, while SMDs offer ...
Comminution represents up to 50% of the total energy consumption in the mineral production process [2]. Moreover, comminution using ball milling is highly inefficient due to heat and mechanical ...
The ball-mill data were analyzed by means of the ore-specific breakage distribution function determined from pendulum tests and a multi-segment ball-mill model, enabling a scale-up relationship to ...
The specific energies of the SAG and ball mills were determined using AusGrind (Ausenco's in-house software) (Lane, Foggiatto, Bueno and McLean, 2013 and Morrell's ) method. SAG mill specific energy was a function of the inverse of the Axb value, the mill geometry and the mill operating conditions.
The size specific energy (SSE) achieved while processing each ore was also calculated based on these plant surveys (JKMRC, 2018). The SSE represents the energy required from the comminution ...
حقوق النشر © 2024.Artom كل الحقوق محفوظة.خريطة الموقع