Effect of ball mill grinding parameters of hydrated lime …
mill speed, 40% ball charge, 25% charged material volume, and 45 min grinding period, the hydrated lime micronization was developed more harmonious distribution curves.
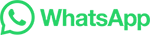
mill speed, 40% ball charge, 25% charged material volume, and 45 min grinding period, the hydrated lime micronization was developed more harmonious distribution curves.
The ball charge consisted of equal number of 1.27, 1.90 and 2.54 cm balls. The mill was run at a speed that corresponded to 70% of the critical speed. The ball load, J, expressed as fraction of the mill volume occupied by balls at rest, was kept at 0.3.
Ball mills are further characterized by the major differences in the sizes of grinding jars and what ball sizes are readily available. Retsch can supply ball mills with …
In recent research done by AmanNejad and Barani [93] using DEM to investigate the effect of ball size distribution on ball milling, charging the mill speed with 40% small balls and 60% big balls ...
What Is Ball Mill? Ball mill is a very welcoming grinding equipment. It uses the friction between the material and the steel ball or steel column and the rotation of the drum itself to promote the grinding material to reach the ideal particle size, to facilitate the classification and flotation operations in the subsequent process. The ...
Crushed ore is fed to the ball mill through the inlet; a scoop (small screw conveyor) ensures the feed is constant. For both wet and dry ball mills, the ball mill is charged to approximately 33% with balls (range 30-45%). Pulp (crushed ore and water) fills another 15% of the drum's volume so that the total volume of the drum is 50% charged.
6. During grinding, balls themselves wear and are continuosly replaced by new ones so that mill contain balls of various ages and thus of various ages and thus of various sizes Ball mill produces 1 to 50 tonn/hr of powder of which 70 to 90 % will pass through a 200 mesh screen and energy requirment of the ball mill is about 16 kwh/tonn …
Effects of ball mill treatment (0, 2, 4, 6, 8, and 10 min) on the free sulfhydryl (SH) and disulfide (S-S) bonds (a) and surface hydrophobicity (b). Different lower case letters denote ...
PDF | A comprehensive investigation was conducted to delineate the effect of ball size distribution, mill speed, and their interactions on power draw,... | Find, read and cite all the...
The effect of liner/lifter profile on kinetics of batch grinding and the milling capacity in general was assessed using mono-size quartz material of 30 × 40 mesh (−600 + 425 μm) as feed. The liner profiles tested were, (i) bevel with 60° lifter face angle to represent the new liners, (ii) bevel with 45° lifter face angle to represent the ...
This means that during one rotation of the sun wheel, the grinding jar rotates twice in the opposite direction. This speed ratio is very common for Planetary Ball Mills in general. Planetary ball mills with higher energy input and a speed ratio of 1:-2.5 or even 1:-3 are mainly used for mechanochemical applications.
seen, the vertical mill consistently presented lower net specific energy consumption than the ball mills which operate on the same circuit. The averages were 11.3, 11.7 and 6.5 …
key factors affecting mill throughput and grinding efficiency: mill speed, ball loading, and liner lifter face angle (angle between the lifter face in contact with a grinding ball and the lifter base). Its central hypothesis is that face angle drives a ball mill's grinding efficiency and throughput independently of the type of liner used.
To evaluate the primary grinding circuit, four of eight parallel ball mills with their cyclones were selected for sampling. The make-up ball characteristics of each mill are shown in …
The effects of the ball-to-powder diameter ratio (BPDR) and the shape of the powder particles on EDEM simulation results and time in the planetary ball mill was investigated. BPDR was varied from ...
The effect of ball size on the particle size reduction has been investigated first for varying rotation speed of the container. Percent passing and size distributions of the milled Al 2 O 3 powder are shown in Fig. 1, Fig. 2, respectively, as a function of particle size for varying ball size.The average particle sizes (d 50) of the milled Al 2 O 3 powder are …
The effect of non-circularity on both the flow and power draw is evaluated for the case where the mill contains only non-circular steel balls. We use the same configuration as described in Section 9.1 with three discrete ball sizes and allow the balls to have aspect ratios distributed between 1 and 2:1 and super-quadric powers between 2 …
S. M. Salili, A. Ataie, Z. Sadighi; Effect of Ball Size and Ball to Powder Ratio Variation on Crystallite Size and Formation of Nanocrystalline Materials in Planetary Ball Mill. AIP Conf. Proc. 26 December 2011; 1400 (1): 127–130.
The ball mill, liners and grinding media employed were made from stainless steel. ... In this case an example size class of -150 + 75 μm can be selected that will maximize the amount of material for a leaching process. The Figure shows that more of the material is obtained for the three ball mixture. ... The effects of ball filling and ball ...
There are three types of grinding media that are commonly used in ball mills: • steel and other metal balls; • metal cylindrical bodies called cylpebs; • ceramic balls with regular …
Ball mill is one of the most commonly used mills for the crushing and grinding of mineral ore. ... To further examine the effect of mill size on particle ... we investigated the minimum size of training data required for reasonable accuracy. Dataset based on 108 cases was randomly divided into different subsets of training data varying …
The power input required to maintain this condition is theoretically: hp = (W) (C) (Sin a) (2π) (N) 33.000. where W = weight of charge. C = distance of center of gravity or charge from center of mill in feet. a = dynamic angle of repose of the charge. N = mill speed in rpm. The value of the angle a varies with the type of discharge, percent of ...
This paper focuses on the determination of the selection function parameters α, a, μ, and Λ together with the exponent factors η and ξ describing the effect of ball size on milling rate for a South African coal.. A series of batch grinding tests were carried out using three media single sizes, i.e. 30.6, 38.8, and 49.2. mm.. Then two ball mixtures …
In the case of filling with st eel balls, f or all tests with non-standard dimensions, mono size balls of 2.54 cm in diameter were used (2475 cm 3 / 8.58 cm 3 ≈288 steel balls, to min imize the ...
Ball mill is an ef cient tool for grinding materials like ores, chemicals, ceramic raw materials, paints etc. into ne powder or ne paste by grinding in a wet way. The Ball Mill operates by rotating a cylinder with grinding balls like steel, CI, ceramic and pebble balls as grinding media. Material fed through the mill is crushed by impact and ...
Effect of particulate environment on the grinding kinetics of mixtures of minerals in ball mills. Author links open overlay panel V.K. Gupta. Show more. Add to Mendeley. ... in the case of hematite, the weight % values for the 840/595 and 420/297 μm size classes differ by 10–13% from those observed in the case of calcite and quartz. Due …
optimisation of grinding equipment such as ball mills can provide significant cost and CO 2 ... crusher settings but are in some cases still up to 50mm when fed to the ball mill and …
Particle size reduction of materials in a ball mill with the presence of metallic balls or other media dates back to the late 1800's. The basic construction of a ball mill is a cylindrical container with journals at its axis. The cylinder is filled with grinding media (ceramic or metallic balls or rods), the product to be ground is added and ...
[7] N. Hlabangana, G. Danha, E. Muzenda, Effect of ball and feed particle size distribution on th e milling efficiency of a ball mill: An attainable region approach, South African Journal [1] of ...
In these cases, the feed to the ball mill may be from 10 to 100 mesh or even finer. ... Also applicable for very viscous material and humidities of 3—15 % by weight. Overflow Ball Mill: ... A load of rods has more of a rolling and less of a cascading motion than a load of balls, and the shattering effect of the rods on the ore is consequently ...
حقوق النشر © 2024.Artom كل الحقوق محفوظة.خريطة الموقع