Coke Reactivity in Simulated Blast Furnace Shaft Conditions
Larger sized coke (grain size 4.67 to 6 mm) was used in estimating the correlation between reactivity in 100 pct CO 2 and the simulated blast furnace shaft gas atmospheres, since it also includes the effects of macroporosity and the reaction mechanism is closer to the actual sized coke. The grains were prepared by crushing …
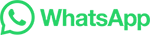